روش های کنترل بو در تأسیسات تولید کمپوست
مزاحمت هایی که به طور معمول از سوی یک واحد تولید کمپوست متوجه مناطق مسکونی و سایر مراکز تمرکز جمعیتی واقع در اطراف این تأسیسات میشوند، شامل بوهای نامطلوب، گرد و غبار، رشد و نمو حشرات و جلب پرندگان و جوندگان موذی است. در این مقاله از دی مگ به بررسی روش های کنترل بو در تأسیسات تولید کمپوست می پردازیم.
شکی نیست که در بین موارد گفته شده تولید بوهای نامطلوب و آزاردهنده به عنوان بزرگترین مشکل این نوع تأسیسات بوده و مهم ترین اعتراضهای مردمی، مربوط به این مورد است. بیشتر مشکلات تولید بو نیز ناشی از عدم توجه کافی به بحث مدیریت و نگهداری و بهره برداری تأسیسات و عدم پیش بینی تمهیدات لازم به منظور کنترل بوهای نامطلوب است. در برخی موارد نیز لزوم انجام طراحی مجدد در تأسیسات موجود، که هزینه های زیادی نیز دربر دارد مربوط به حل مشکلات تولید بو، خواهد بود.
علل ایجاد بو در تولید کمپوست و ترکیبات مولد آن
تمام موجودات زنده، گیاهان و جانوران کم وبیش مولکولهای بوزا از خود ترشح میکنند. از طرف دیگر نیز تمام مواد خام و اولیه مورد استفاده برای تولید کمپوست از راه های مختلف از گیاهان و جانوران بدست آمده است. بنابراین این مواد به صورت بالقوه دارای توان تولید بوهای مختلف مطبوع یا نامطبوع اند. حتی در صورتی که مواد خام اولیه دارای مولکولهای بوزا نیز نباشند، متابولیسم های بیوشیمیایی صورت گرفته در مراحل مختلف تجزیه میکروبی کمپوست، مواد بینابینی بیشمار را تولید می کنند که دارای بو هستند.
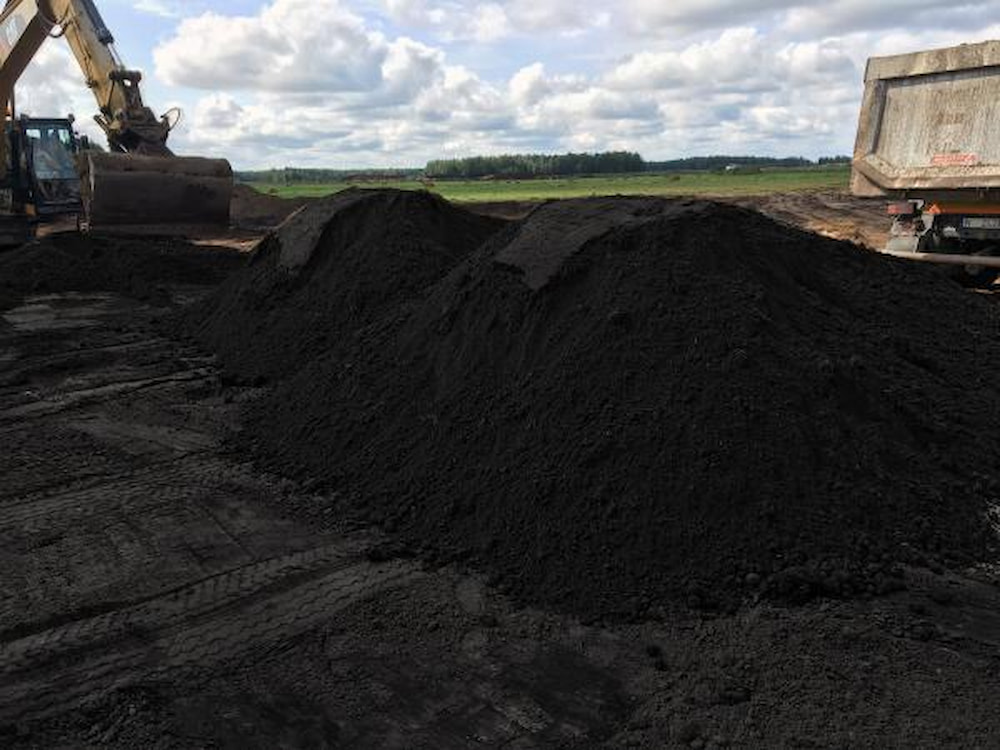
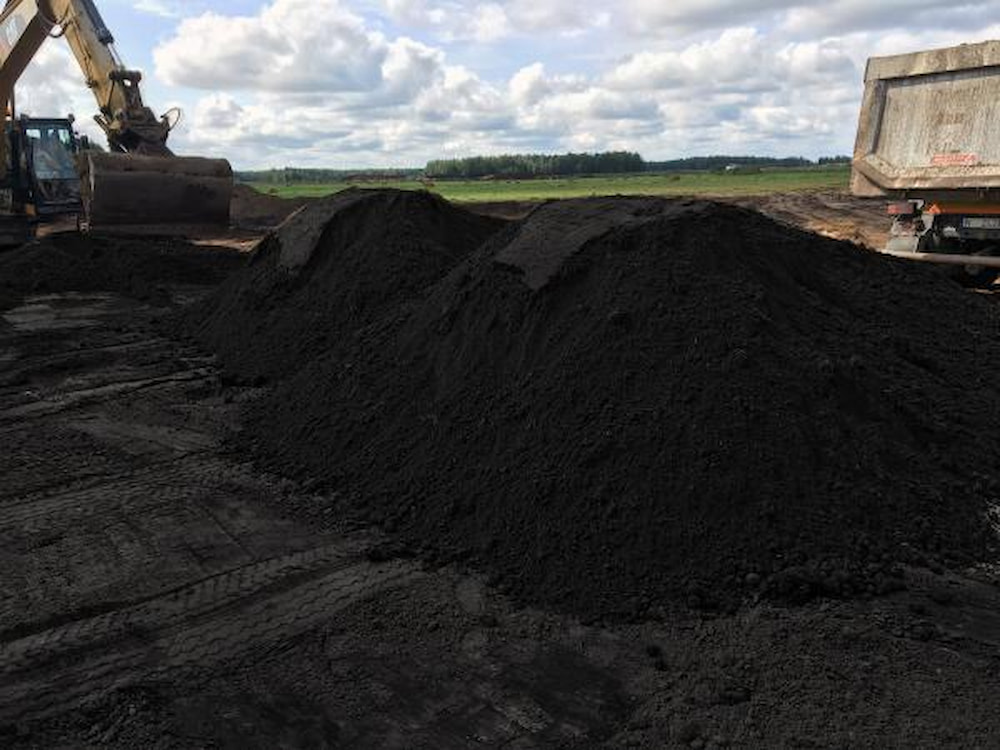
روش های کنترل بو در تأسیسات تولید کمپوست
برخی از این ترکیبات که از متابولیسم بی هوازی مواد خام حاصل میشوند، شامل سولفید هیدروژن اسیدهای آلی، فرار مرکاپتانها و متیل سولفیدها هستند. بسیاری بر این باورند که اگر فرایند تولید کمپوست به طور کامل هوازی باشد، هیچ گونه بوی نامطلوبی ایجاد نخواهد شد. در حالی که این موضوع واقعیت ندارد. بسیاری از ترکیبات بینابینی مولد بو با وزن مولکولی کم (فرار) حتی در حین کمپوست سازی هوازی نیز تولید میشوند. آمونیاک، اسید استیک اسید پیروویک و اسید سیتریک از جمله این مواد هستند. این نوع ترکیبات در مقایسه با ترکیبات تولید شده در طی فرایند تجزیه بی هوازی کمتر آزار دهنده بوده است ولی بدون بو هم نیستند.
ترکیبات مولد بو در تاسیسات تولید کمپوست
ترکیبات مولد بو در تولید کمپوست به طور معمول در ۷ دسته کلی شامل:
- اسیدهای چرب فرار (اسیدهای استیک، پروپیونیک و بوتیریک که به سادگی قابل تجزیه هستند)،
- آمینها (متیل آمین، اتیل آمین دی متیل آمین و تری اتیل آمین که بسیار بدبو و بوی شبیه ماهی یا تعفن دارند)،
- ترکیبات حلقوی معطر (ایندول و اسکاتول که بوی بسیار بدی داشته و بر اثر تجزیه بی هوازی مواد پروتئینی ایجاد می شوند)،
- سولفیدهای معدنی (سولفید هیدروژن)،
- سولفیدهای آلی (مرکاپتانها که از اسیدهای آمینه گوگرددار هم در شرایط هوازی و هم در شرایط بی هوازی تولید میشوند)،
- ترپن ها (از تجزیه مواد چوبی و گیاهان ایجاد میشوند آمونیاک تجزیه هوازی یا بی هوازی پروتئینها و اسیدهای آمینه حاصل میشود)
- سایر مواد مولد بو، آلدئیدها، الکل ها، ستن ها، آلکنها، اترها، استرها، آکریلاتها، بوتیراتها و غیره طبقه بندی میشوند.
همان گونه که گفته شد بخش مهم مواد مولد بو در تاسیسات کمپوست، در اثر رخداد شرایط بی هوازی در توده کمپوست تولید شده است و از این رو حفظ شرایط در حالت هوازی تا حدود زیادی در کاهش تولید بو مؤثر خواهد بود.
روش های کنترل بو در تاسیسات کمپوست
مهم ترین و مؤثرترین روش کنترل بو در طی فرآیند تولید کمپوست به روش هوازی با انجام تمهیداتی مانند ایجاد توده کمپوست با مشخصات فنی صحیح بویژه از لحاظ ارتفاع توده که باید از حد مشخصی کمتر باشد و هوادهی مرتب و منظم آن بخصوص با زیر و رو کردن صحیح مرتب و منظم توده و به طور کلی مدیریت بهره برداری و نگهداری مناسب تأسیسات تولید کمپوست است.
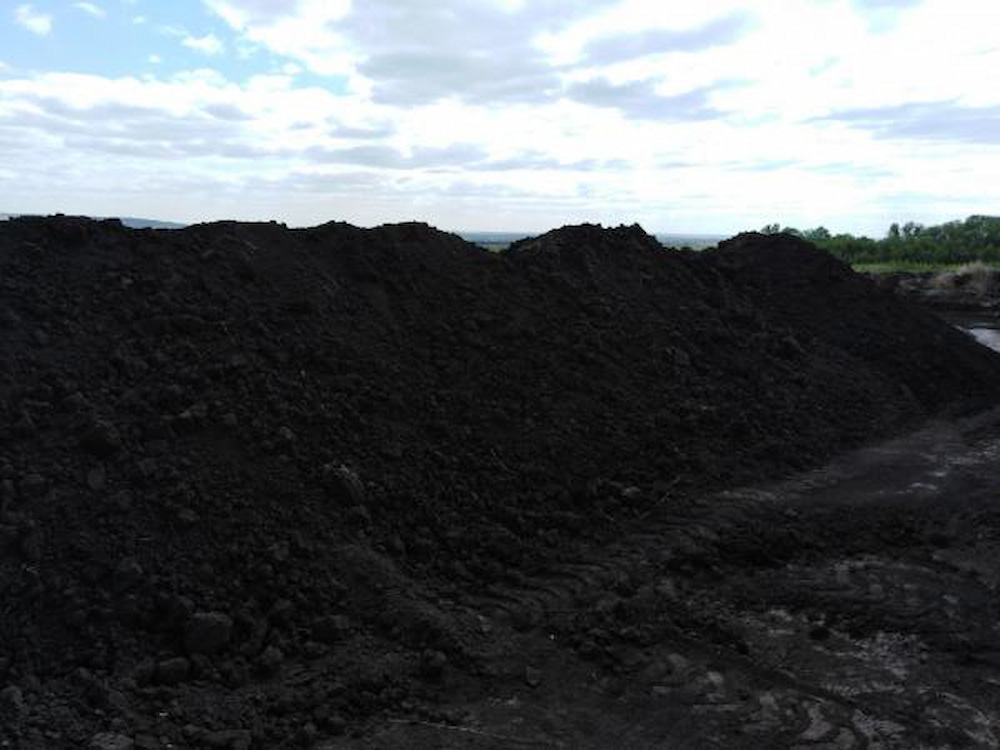
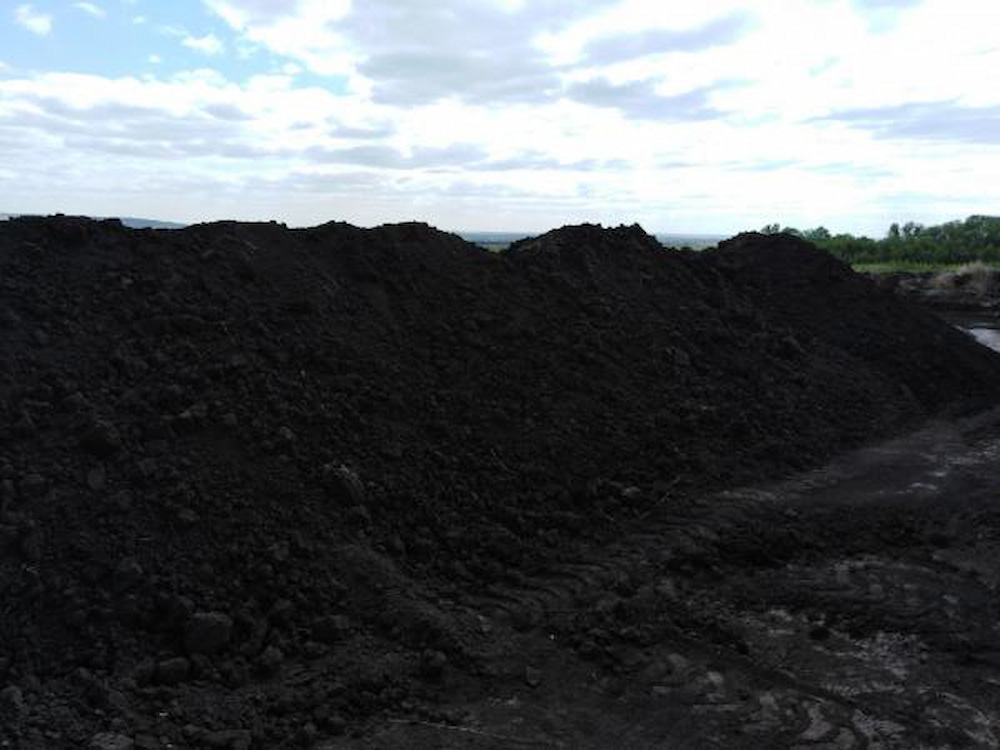
روش کنترل بو در تولید کمپوست
اما همان گونه که گفته شد در فرایند به طور کامل هوازی تولید کمپوست نیز بوهای آزاردهنده هر چند در حد کم تولید می شود و افزون بر آن بسیار امکان دارد که بر اثر ایجاد مشکلات مختلف در حین بهره برداری، شرایط تولید کمپوست به حالت بی هوازی نزدیک و یا به طور کامل بی هوازی شده و در نتیجه باز هم امکان دارد تولید این نوع بوها وجود داشته باشد. بنابراین استفاده از تجهیزات و دستگاه های مختلف کنترل بو در تأسیسات تولید کمپوست ضرورت دارد. البته رعایت نکات فنی و مهندسی در مورد مکان یابی تأسیسات کمپوست بویژه از نظر فاصلهٔ آن از مراکز جمعیتی و توجه به جهت وزش بادهای صحیح غالب نیز بسیار ضروری است.
در هر صورت روش ها و تجهیزات مختلف متداول در کنترل بو شامل:
- جذب،
- جذب سطحی
- اکسیداسیون گرمایی،
- اکسیداسیون شیمیایی،
- اکسیداسیون بیولوژیکی (صافیهای زیستی)
- و در نهایت پوشش دادن و خنثی سازی است.
البته برای امکان کاربرد این روشها لازم است که سالن تخمیر کمپوست سر پوشیده و مجهز به هواکشهایی شود که گازهای بدبو را جمع آوری و به این تجهیزات هدایت می کنند.
۱- جذب
در روش جذب، ترکیبات مولد بو در یک مایع جاذب شوینده حل می شود. فناوری های به کار رفته در این روش، شامل برجهای آبپاش یا بخارساز، شوینده های بستر آکنده، طرح های ترکیبی و در نهایت میعان – خنک سازی هستند. مواد شیمیایی متداول مورد استفاده به عنوان مایع جاذب نیز شامل:
- مواد اکسیدکننده (هیپوکلریت سدیم پراکسید هیدروژن (H202) و پر منگنات پتاسیم)؛
- مواد قلیایی (آهک، آب آهک و سود سوزآور)؛
- مواد اسیدی (اسید سولفوریک و اسید کلریدریک)؛
- مواد تقویت کننده جذب (سورفاکتانتها)
-
برجهای بخارساز
این برج ها به صورت سه مرحله ای کار میکنند و محلول مواد شیمیایی به صورت بخار و یا اسپری وارد هر مرحله از برجها میشود. در مرحله اول با تزریق محلول اسید سولفوریک، آمونیاک خنثی می شود. در مرحله دوم نیز اکسیدکننده (هیپوکلریت سدیم) برای حذف سولفیدهای آلی و سایر مواد آلی ترینها به کار میرود در مرحله سوم نیز گازهای خروجی مرحله دوم به وسیله مواد احیاکننده پراکسید هیدروژن و بی سولفیت سدیم، کلرزدایی میشوند.
-
شوینده های بستر آکنده
این روش نیز سه مرحله ای است. در مرحله اول از پساب تصفیه خانه فاضلاب، به عنوان بستر جاذب آمونیاک استفاده شده و برای بهبود فرایند مقداری اسید سولفوریک به پساب افزوده میشود. در مرحله دوم از هیپوکلریت سدیم برای حذف سولفیدهای آلی استفاده شده و مقداری سورفاکتانت نیز به منظور حذف بیشتر هیدروکربورها به آن اضافه میشود. مرحله سوم نیز شامل حذف کلر اضافی مرحله دوم با پر اکسید هیدروژن است.
-
طرحهای ترکیبی
این روش ترکیبی است از دو روش برجهای بخارساز و شوینده های بستر آکنده، به گونه ای که مزایای هر دو را داشته و معایب هیچ کدام از آنها را نداشته باشند.
-
میعان و خنک سازی
در این روش از مایع سازی بخار آب دارای گازهای مولد بو استفاده می شود. گازهای تولیدی از کمپوست، به طور معمول دارای بخار آب است و بنابراین بخار آب آلوده از میان فضاهای بین صفحات و لوله های سرد عبور میکند و همراه با گازهای بد بوی درون آن تبدیل به مایع شده و جداسازی میشود.
۲- جذب سطحی
در این روش از ویژگی جذب سطحی بسیار زیاد کربن فعال در حذف گازهای مولد بو استفاده می شود.
۳- اکسیداسیون حرارتی
در این روش گازهای مولد بو در درجه حرارتهای زیاد ۶۵۰۸۵۰ درجه سانتی گراد سوزانیده میشوند این روش نیاز به انرژی حرارتی زیادی دارد.
۴- اکسیداسیون شیمیایی
در این روش از محلولهای اکسید کننده شیمیایی همانند آنچه در روش جذب گفته شد، استفاده میشود. تزریق گازهای اکسید کننده مانند ازن به صورت مستقیم درون گازهای مولد بو نیز کاربرد دارد.
۵- اکسیداسیون بیولوژیکی
اکسیداسیون بیولوژیکی متداولترین روش کنترل بو در تأسیسات کمپوست محسوب می شود. البته در بسیاری موارد روشهای جذب و جذب سطحی به عنوان یک راهکار مقدماتی پیش تصفیه بکار رفته و روش غالب همان اکسیداسیون بیولوژیکی است. اکسیداسیون بیولوژیکی به دو روش کاربرد لجن فعال به عنوان یک صافی زیستی مایع و صافیهای زیستی قابل انجام است.
-
لجن فعال
این روش یک صافی زیستی مایع به شمار میرود اساس عملکرد آن، جمع آوری گازهای دارای سولفید هیدروژن، مرکاپتانها و سولفیدهای آلی و اختلاط آن با هوایی است که برای هوادهی سیستم لجن فعال تصفیه فاضلاب شهری به کار می رود.
گازهای مولد بو به وسیله میکروارگانیسمهای سیستم لجن فعال با کارایی ۹۰ درصد، جذب و تجزیه شده است و ۱۰ درصد باقیمانده نیز به جای اینکه به صورت نقطه ای از محل کارخانه آزاد شود، به صورت گسترده از سطح وسیع حوض هوادهی منتشر میشود و از این رو مقدار بوی آن تا حدود زیادی کاهش می یابد.
-
صافی های زیستی
این روش سیستم کنترل آلودگی هوا به شمار میرود که در آن برای جذب یا جذب سطحی گازهای بدبو از جریان هوا و برای اکسیداسیون بیولوژیکی این گازها از بستر جامد زیستی فعال میکروبی استفاده میشود می روند. صافی های زیستی، بیشتر برای حذف ترکیبات آلی فرار (VOC) و عوامل مولد بو از دیرباز استفاده شده اند و امروزه نیز برای کنترل بو در اماکن دفن بهداشتی زباله به کار میروند. فعالیت زیستی خاک در مقایسه با بسترهای دیگر مانند پیت و کمپوست معمولی بسیار کمتر بوده و لذا برای بارگذاری کم مناسب است.
در سیستم صافیهای زیستی، ابتدا گازهای مولد بو پیش از ورود به صافی از نظر رطوبت تنظیم شده و یک سیستم چندلایه ای سبب توزیع مناسب گاز در کل نقاط صافی می شود. عمق صافی در حدود ۱۱/۵ متر است.
مشکلات صافیهای زیستی:
- بارگذاری آنها باید کم باشد، در غیر این صورت بازده به شدت کاهش می یابد.
- یک روش تصفیه زیستی به شمار می رود و از این رو شرایط لازم برای عملکرد بهینه آن برای مثال رطوبت و pH باید به دقت کنترل شوند.
- راندمان حذف بو هیچگاه ۱۰۰ درصد نیست و مقداری بو آزاد می شود. خود صافی نیز، در صورت بهره برداری نامناسب ممکن است عامل تولید بو باشد، بویژه اگر از خود کمپوست به عنوان بستر صافی استفاده شود.
نکات صافیهای زیستی در روش اکسیداسیون بیولوژیکی
- بستر صافیهای زیستی باید تمام مواد مغذی لازم برای رشد و تکثیر باکتریهای مؤثر بر تجزیه عوامل مولد را داشته باشند. ترکیبات مولد بو، به طور معمول دارای منبع انرژی و کربن مورد نیاز سلول سازی به شکل ترکیبات آلی هستند و فقط افزودن نیتروژن و تا حدودی فسفر به آن ضرورت دارد.
- دمای بستر صافیهای زیستی باید در محدودهٔ سرما دوست و مزوفیلیک ۳۵-۱۵ درجه سانتی گراد نگه داشته شوند. دماهای خیلی کم، سبب کاهش شدید سرعت فرایند می شوند و دماهای زیاد (گرمادوست) نیز تنوع میکروبی بستر صافی را کمتر میکنند.
- اکسیداسیون آمونیاک، سولفید هیدروژن و سولفیدهای آلی درون بستر صافی زیستی می تواند سبب ایجاد شرایط اسیدی و کاهش مقدار pH به حدود ۳-۱ شود. البته در مورد تصفیه سولفید هیدروژن، این مسئله مشکل ساز نبوده است و باکتریهای اکسید کننده گوگرد بویژه تیوباسیل ها شرایط اسیدی را دوست دارند. ولی در صورت وجود سایر مواد مولد بو در جریان گازهای ورودی شرایط اسیدی سبب کاهش شدید راندمان حذف آنها میشود. بنابراین لازم است مقدار pH در صافی های زیستی در حدود ۸/۵-۷ نگه داشته شود.
- در صورت ایجاد شرایط اسیدی در بستر صافی میتوان بستر را تعویض و یا از آهک و سایر مواد قلیایی به منظور اصلاح pH استفاده کرد. روش دیگر جلوگیری از ایجاد شرایط اسیدی، حذف عوامل مولد اسیدیته قبل از ورود به صافی است.
جنس بستر صافی های زیستی
بستر صافی های زیستی را میتوان از انواع کمپوست گرفته تا مخلوطهایی که از اختلاط کمپوست، خاک پیت، چوب، آهک، کربن فعال و دانه های پلی استیرن درست میشوند، انتخاب کرد. بستر باید ویژگیهای مکانیکی و فیزیکی مناسب داشته باشد تا هزینه های بهره برداری و نگهداری آن کاهش پیدا کند. همچنین آب را به راحتی از خود عبور دهد تا از آب گرفتگی هم جلوگیری شود. همچنین نباید در طول زمان متراکم شود تا افت فشار هوا هنگام عبور از آن به وجود آید و ویژگیهای شیمیایی و بیولوژیکی لازم برای زندگی میکروبها را داشته باشد و از طرف دیگر آنقدر پایدار نباشد که به مرگ باکتری ها بر اثر گرسنگی بینجامد.
میکروبهای صافیهای زیستی نیاز به بستری مرطوب دارند و بسترهای خشک فعالیت آنها را تا حدود زیادی کاهش میدهد. رطوبت مناسب بستر صافی ۷۰-۵۰ درصد بوده و افزون بر آن باید رطوبت را نیز حفظ کند. تراشه های چوب و سایر مواد مشابه علاوه بر ایجاد خلل و فرج لازم برای زهکش آب، بستر را در حد نیاز مرطوب نگه میدارند.
۶- روش پوشش دادن و خنثی سازی جهت جلوگیری از بو در تاسیسات تولید کمپوست
در این روش از تزریق بوهای مطبوع مانند وانیل سیب یا لیمو در هوای کارخانه و یا درون جریان گازهای بدبو به منظور تحت الشعاع قرار دادن آنها استفاده میشود. از مزایای این روش آن است که تجهیزات به کار رفته به سادگی قابل تهیه و حمل بوده و هزینه کمی را در بر دارد.
خنثی سازی، نیز روشی است که در آن از مواد مخصوصی نظیر آمین ها، مرکاپتانها، آلدییدها و ترکیبات حلقوی معطر برای خنثی سازی یا کاهش بوهای نامطبوع به روش مشابه با روش معطرسازی پوشش دادن استفاده میشود.
برای دانستن مطالب بیشتر در این زمینه کلیک کنید:
مواد سمی کود کمپوست و اثرات سوء آن بر رشد گیاهان و محیط زیست
دیدگاهتان را بنویسید